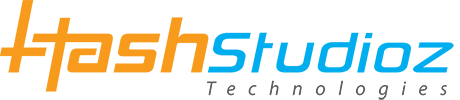
- About Us
- Our Services
- Solution
- Products
- Hire
- Technologies
- Industries
- Resources
- Contact Us
The need of gathering operational data is very important for a manufacturing facility as the cost of the entire product and the profitability of the business as well as ROI is calculated based on it. Since the automation and computerization of almost all the production units, and the standardization of the protocols used for the communication between the device, It has become an urge for the administrators to take all the production data online and use a dashboarding tool and sometimes with AI capabilities to visualize the data and do predictions of system health and cost projections for the item being manufactured.
RS485 modbus communication is an industry standard when it comes to industrial automation. It makes communication between two devices possible over considerable distances inside a factory. But RS485 communication is prevalent only amongst PLC and CNC devices only. For Humans, we need the data taken up to a dashboard and processed so that a useful information set can be presented to the user. The Modbus RS485 to MQTT gateway provides one such interface to the dashboard service. It extracts the data from the MODBUS data lines and transmits the packet over MQTT to the dashboard service.
The Spring forming machine is one of the marvels of engineering which facilitates proper functionality of devices ranging from common ball point pens to the super complex Internal Combustion engine and much more. The manufacturer had a series of machines producing springs at speeds of 100-200 springs per minute. And with 4 types of different machines and 3-4 of each type, it is a daunting task to track orders and production status. Chances of human error and deadline overshoot are something which needs to be checked especially with the production happening round the clock and 3 different shifts of people keeping the production running.
The dashboard and machines keep track of batches of products being drawn and the RS485 gateway helps in connecting the machine to the dashboard. With all the data in the dashboard,. The manufacturer can even give real time order updates on the order to its client. Moreover the administration, production control and quality control departments can work on the data provided by the machines and keep the quality consistent across the production batches.
A simplistic dashboard depicting the Production speeds and batch being produced on each of them is available for the administrators, A panel with the totals of production volumes against each order is visible to the sales team for providing the insights of the production to the end customers. A panel with overall production and machine operational status along with the batch counts is available to the Quality Analysis team so they can collect and analyze the quality across the batch of products being formed.
We developed a MQTT based solution which can collect data from the machines and transmits the data on to a database backed Dashboard. An API endpoint is also required by the manufacturer so the data can be received and displayed by a third party CRM. The authentication based API exposes data to the Client, segregated by the type of product in production at the moment and the client is able to view just the product for which he has placed the order.