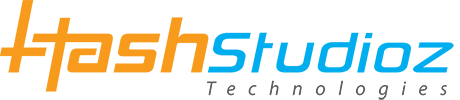
- About Us
- Our Services
- Solution
- Products
- Hire
- Technologies
- Industries
- Resources
- Contact Us
This case study highlights a live project consulted and undertaken by HashStudioz to reduce manual work of Factory Supervisors pertaining to testing of mechatronic components and reporting of results. This not only resulted in facilitating increased production capacity and manpower capacity but also led to freeing up of skilled supervisors from monotonous labor-like tasks for their better utilization in more self-fulfilling, decision-making and intelligent purposes..
The organization belongs to manufacturing factory domain and essentially manufactures bottles on a large scale. It started facing hurdles for its large scale Asia-Pacific expansion plans as it required more manpower owing to its manual nature of supervisory jobs.
On reviewing the issue we found that it wasn’t the strategic decision that was at fault but needed a major process revamp for optimization. Being an experienced team of Industry4.0 and IoT projects, we undertook this project and designed an industrial automation solution to eliminate the manual part and reduce skilled man-hours considerably.
We designed an ICT enabled embedded system to test various parameters like Inductance, Resistance, Holding Currents and Feedback Voltage from Motor.
Factually, testing these parameters of motor took a fair amount of time of 20-30 mins and supervisors had to do it manually and write down all the observations at the end of every 30 minute cycle.
To address this, our in house designed and developed kit delivered them an automated testing of the motors which completed end-to-end testing of all parameters in mere 2 minutes, recorded these observations and displayed them in readable GUI format. It could also be saved locally in spreadsheets by end users/supervisors.
This reduced testing cycle time from 30 minutes to 2 minutes and facilitated dual operation-improvement methods for our customer:
1) Increased process productivity by reducing testing time.
2) Increased skilled man-hour capacity utilization by displaying response in custom-tailored GUI and making it downloadable.
The success of customer to successfully mitigate growth barriers and pave an entry into large scale market could be attributed to timely realization about the urgency and need to remodel in-part or in-full its legacy processes. Simple Integral can help you to identify best suited channels and embark on the journey of your digital transformation to be a global leader.