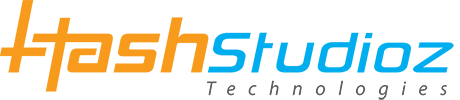
- About Us
- Our Services
- Solution
- Products
- Hire
- Technologies
- Industries
- Resources
- Contact Us
This case study explores the implementation of an Industrial Automation use case at a Spring manufacturing factory, where data from machines was captured using various sensors over Modbus communication and transmitted to the cloud using an IoT Gateway over a 4G LTE network. The collective data is presented on an immersive dashboard, allowing stakeholders to monitor critical parameters such as individual machine health and overall production.
An established spring manufacturer has been producing a wide range of springs for various industrial applications for several decades. Despite their significant market presence, they faced challenges optimizing production processes and monitoring machine health.
An end-to-end Industrial IoT solution was designed and implemented to address the client's challenges, incorporating the following key components:
A variety of sensors were integrated into the machines using the Modbus communication protocol, enabling seamless data exchange.
An IoT Gateway was installed to collect data from the sensors and act as an intermediary between the machines and the cloud platform. The gateway was equipped with 4G LTE connectivity, ensuring reliable and fast data transmission to the cloud server.
The collected data was securely transmitted to the cloud platform, where it was stored and processed. Advanced data analytics algorithms were applied to extract valuable insights from the data.
A user-friendly and visually appealing dashboard was developed, displaying real-time data on machine health and production output. Key performance indicators (KPIs) such as machine uptime, units produced, and overall equipment efficiency (OEE) were prominently showcased.
The implementation of the Industrial IoT solution resulted in several significant benefits for the client:
The implementation of an IIoT solution allowed the client to have global access to data.
Predictive maintenance based on machine health data helped reduce maintenance costs by addressing issues before they escalated into major problems.
Real-time monitoring and analysis of critical parameters ensured consistent product quality and adherence to specifications.
Improved efficiency and quality of production led to faster delivery times and better customer satisfaction, positively impacting the client's reputation.
The ability to monitor production output in real-time enabled the client to identify bottlenecks and optimize processes, leading to increased productivity and overall efficiency.
Data analytics provided valuable insights into production patterns and machine behavior, empowering stakeholders to make data-driven decisions for process improvement and resource allocation.
With data from sensors transmitted in real-time to the cloud, the client gained continuous visibility into the health and performance of their machines. This allowed for proactive maintenance and minimized unplanned downtime.